1. Kalitesiz
Malzeme, takım tasarımı, ısıl işlem, işleme doğruluğu, boya kalitesi vb. Standart değildir, bu da kolayca kırılmaya yol açabilir. Örneğin, dokunurken, hareketli boyut farkı çok büyüktür, geçiş filetosu tasarlanmamıştır, stres yoğunlaşır ve kırılması kolaydır. Eklemin sap ve alet arasındaki kesitsel transferi, kaynak kraterine çok yakındır, bu da kesit transferinde kaynak gerilimi ve stres konsantrasyonunun karmaşık örtüşmesine neden olur, bu da büyük bir stres konsantrasyonu ve TAP'a zarar verir. kullanımda.
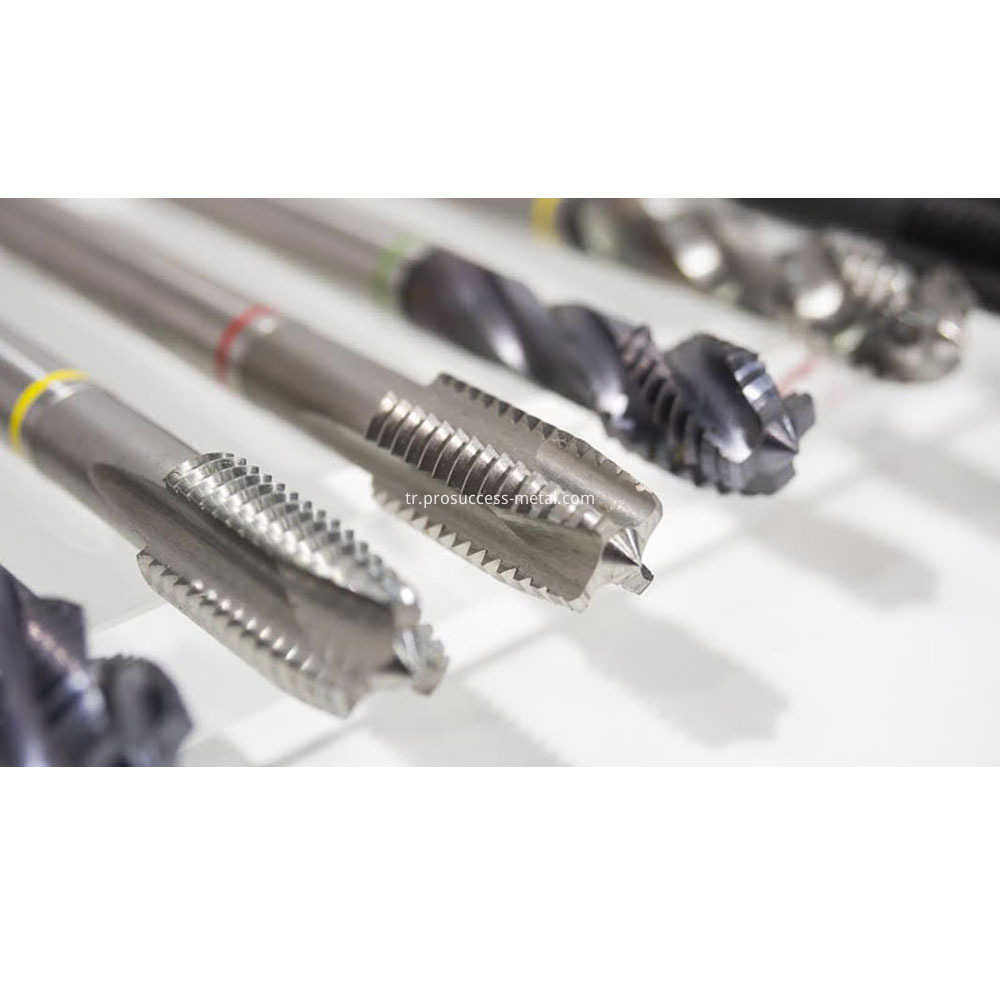
2. Mantıksız seçim
Yüksek sertliğe sahip parçaları dokunmak için, yüksek hızlı çelik musluklar, karbür muslukları, kaplamalı musluklar vb. Gibi yüksek kaliteli musluklar seçilmelidir.
3. Dokunma araçları, malzemelerin işlenmesi için uygun değildir
Son yıllarda, bu sorun giderek daha fazla ilgi gördü. Geçmişte, yerli üreticiler her zaman ithal dokunma araçlarını iyi ve pahalı olarak görmüşlerdir. Ama aslında, birçok yerli dokunma aracı çok uygundur. Yeni malzemelerin sürekli artışı ve işleme zorluğu ile, bu talebi karşılamak için çeşitli araçların malzemeleri de artmaktadır.
4. Alt deliğin delik çapı çok küçük
Örneğin, 0,5 mm'lik bir kesme fişi kullanılırken, demir tabanı M5X işleyerek seçilen 4,5 mm çapında matkap ucu ile alt deliği delin. 4.2 mm çapında bir matkap deliği kullanılırsa, dokunma işlemi sırasında musluğun kesme kısmı artmalı ve musluk kırılacaktır. Dokunma türüne ve dokunulmuş parçanın malzemesine bağlı olarak, doğru delinmiş delik çapını seçmek en iyisidir. Tam nitelikli bir matkap mevcut değilse, daha büyük bir matkap seçilebilir.
5. Konum Sorunları
Dokunmuş kısım kirli malzemeden yapılmıştır ve sağlam bir yer veya deliğe sahiptir. Ve hemen son denge ve yıkımdan çıkıyor.
6. Makine tezgahı, dokunma doğruluğunun gereksinimlerini karşılamıyor
Mekanik aletler ve sıkıştırma gövdeleri de, özellikle yüksek kaliteli musluklar için çok önemlidir. Sadece takım tezgahları ve belirli bir hassasiyete sahip sıkıştırma gövdeleri musluk görevi görebilir. Yetersiz özensizlik yaygındır. Dokunmanın başlangıcında, dokunmanın başlatılması ve konumlandırılması yanlıştır, yani ana şaft alt deliğin merkez çizgisi ile eşmerkezli değildir, ancak musluklar arasındaki tork çok büyüktür, bu da ana nedenidir. dokunmanın kırılması.
7. Kesme Yağı ve Yağlama Yağı Kalitesi
Birçok yerli şirket buna dikkat etmeye başlıyor. Yurtdışında kesme aletleri ve takım tezgahları satın alan birçok şirket çok derin deneyime sahiptir. Kesme yağı ve yağlama yağı kalitesi ile ilgili sorunlar vardır ve işlenmiş ürünlerin kalitesi çapaklara ve diğer olumsuz koşullara eğilimlidir. Aynı zamanda, hizmet ömrü büyük ölçüde kısaltılır.
8. Mantıksız kesme hızı ve besleme hızı
İşlemde bir sorun olduğunda, çoğu yerli kullanıcı kesme hızını ve besleme hızını azalttığından, musluğun itici gücü azalır ve üretilen ipliğin hassasiyeti büyük ölçüde azalır. Sonuç olarak, iplik yüzeyinin pürüzlülüğü artar ve dişli açıklık ve iplik hassasiyeti kontrol edilemez. Tabii ki, Boltz gibi sorunlar daha kaçınılmaz. Bununla birlikte, çok hızlı beslenmek musluk hasarına ve aşırı torka neden olabilir. Mekanik dokunmada kesme hızı genellikle çelik için 6 ~ 15m/dakika, söndürülmüş ve temperli çelik ve sert çelik için 5 ~ 10m/dakika, paslanmaz çelik için 2 ~ 7m/dakika ve dökme demir için 8 ~ 10m/dakika'dir. Aynı malzemede, daha küçük musluk çapları için daha yüksek değerler ve daha büyük musluk çapları için daha düşük değerler kullanın.
9. Operatörün teknolojisi ve becerileri gereksinimleri karşılamıyor
Yukarıdaki konular operatör yargısı veya teknisyenlerden geri bildirim gerektirir, ancak çoğu yerli operatör şu anda bu konulara yeterince dikkat etmemektedir. Örneğin, kör delik iplikleri ile uğraşırken, musluk deliğin altına temas ettiğinde, operatör deliğin altına ulaşmadan önce dokunma hızında beslenmez veya yonga çıkarma düzensiz olduğunda beslenmeye zorlanır , musluğun kırılmasına neden olur. Operatörlerin sorumluluk duygusunu artırmaları gerekir.
Yukarıdakilerden, takım tezgahlarına, fikstürlere, iş parçalarına, süreçlere, aynalmaya ve dokunmaya (araçlar gibi) zarar vermenin birçok nedeni olduğu görülebilir.